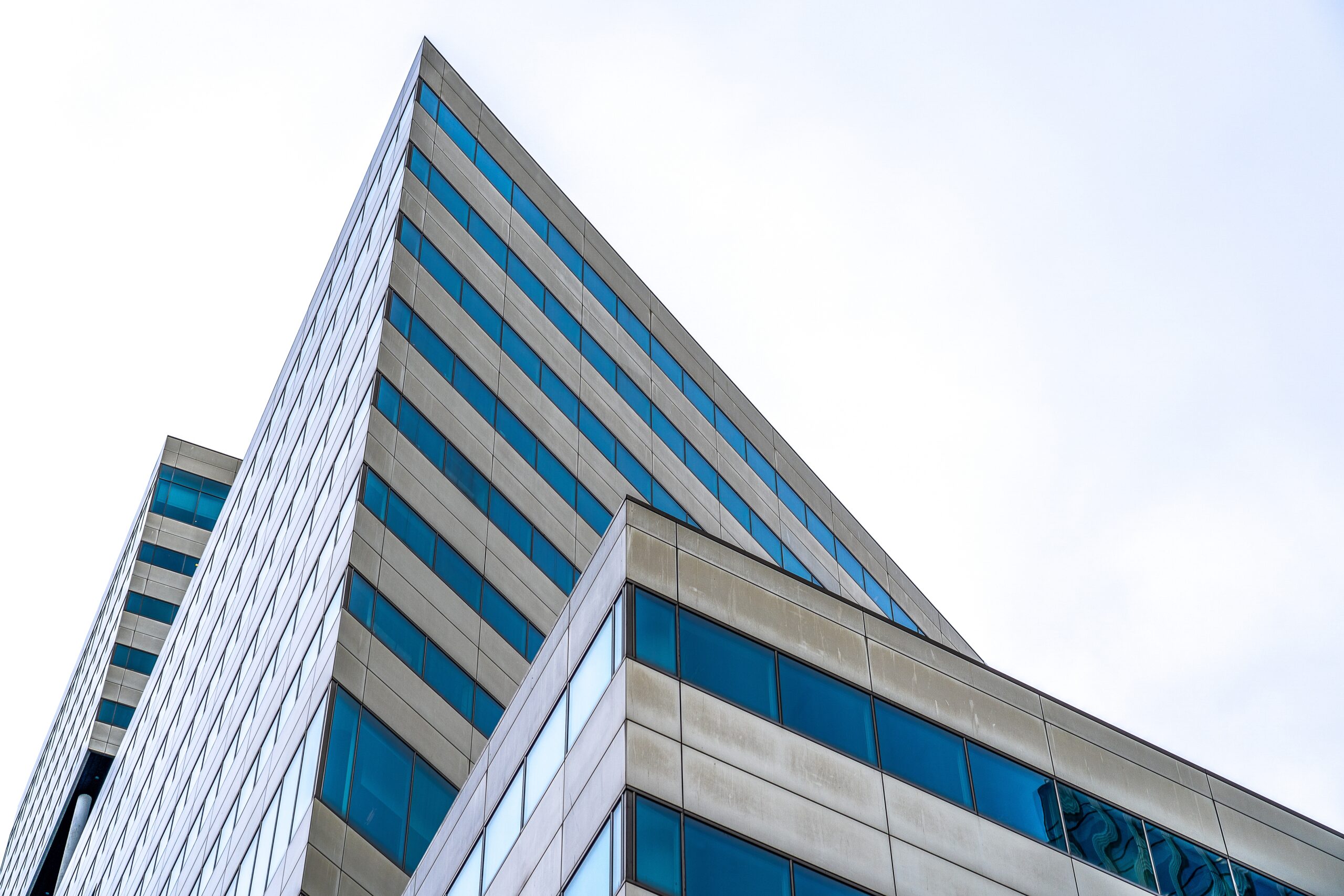
Investing in a commercial roof is a significant decision that offers long-term benefits when protected appropriately. Particularly in regions like Palmetto and Bradenton, where harsh weather can take a toll on structural integrity, roof coatings stand out as a valuable option for sustainable management. These coatings aren’t just an extra layer; they are strategic enhancements ensuring durability, energy efficiency, and cost savings over time.
Understanding the financial and operational implications of roof coatings can profoundly impact a property’s maintenance strategy. Not only do they extend roof life and enhance thermal properties, but they also present a practical means to align with sustainability initiatives. This initial investment in roof coatings pays dividends by lowering energy costs, preventing future repair expenses, and minimizing disruption to business activities. Let’s delve deeper into how choosing the right roof coating can safeguard your commercial property while contributing to a more sustainable future.
Coating Benefits: Enhancing Durability and Energy Efficiency
Commercial roofing is a vital investment for any building owner, especially in places like Palmetto where the climate can be harsh. Protecting that investment with roof coatings can offer numerous benefits, such as enhancing both durability and energy efficiency.
One of the primary advantages of roof coatings is the longevity they add. These coatings create a protective barrier against environmental damage. According to a study published in the Journal of Architectural Engineering, roof coatings can extend roof life by up to 20 years. This is achieved by reducing the potential for leaks and the detrimental effects of UV radiation, rain, and thermal expansion.
Moreover, energy efficiency is a crucial consideration for any commercial building. Roof coatings reflect sunlight, which reduces heat absorption and helps keep indoor temperatures stable. A study by the Lawrence Berkeley National Laboratory found that reflective roof coatings can lower roof temperatures by up to 60 degrees Fahrenheit. As a result, less energy is required for air conditioning, which can lead to significant savings on energy bills. This is especially beneficial for a region like Palmetto, where summers are hot and can lead to increased cooling costs.
Let’s explore how thermal reflectivity of roof coatings directly impacts utility expenses. Data from the Cool Roof Rating Council indicates that buildings with reflective coatings can reduce energy use by 15-30% during peak cooling months. When applied on a broad scale across commercial properties, these savings can not only improve the bottom line but also contribute to a lower carbon footprint, aligning with sustainability goals.
In addition to these benefits, roof coatings can help prevent costly repairs. Coatings often seal minor existing damage, helping to avoid larger issues that may require extensive repair work. A report by the National Roofing Contractors Association suggests that even small, preventive measures like coatings can significantly reduce repair costs over time. By maintaining the structural integrity of the roof, property owners ensure the safety of their tenants and the smooth operation of their businesses.
Furthermore, applying a roof coating can be less disruptive than a full roof replacement. Commercial operations in Palmetto, ranging from retail to warehousing, can suffer major setbacks during extended construction periods. An article from FacilitiesNet highlighted that applying a coating is quicker and often more cost-effective, mitigating disruption and allowing businesses to continue their operations with minimal interference.
Consideration of environmental impacts is more relevant than ever. Many roof coatings are manufactured with environmentally friendly materials designed to minimize their ecological footprint. For example, water-based coatings have been shown to release fewer volatile organic compounds (VOCs), a factor emphasized in research by the Environmental Protection Agency as significant for reducing air pollution.
While focusing on the benefits, it’s crucial to select the right type of coating for your specific needs. Options such as acrylic, silicone, or polyurethane coatings each come with their unique properties suited for different conditions. For instance, silicone works well in areas with heavy rain due to its water-resistant properties, while acrylic is favored for its UV resistance in sunny climates like Palmetto. Consulting with a certified roofing professional to evaluate specific requirements is advisable.
In summary, investing in commercial roof coatings offers multifaceted benefits. Prolonged durability, enhanced energy efficiency, and reduced maintenance costs make them a smart choice for property owners. As climate considerations become increasingly prevalent in decision-making processes, roof coatings present a practical solution for adapting existing infrastructure to meet energy and environmental goals. As data continue to support their advantages, adopting these measures in Palmetto and beyond not only safeguards investments but also aligns with a more sustainable future.
Types of Coatings: Comparing Materials and Applications
When choosing a roof coating for your commercial property in Manatee County, understanding the types of coatings and their specific benefits can guide you in making the best decision for your building’s needs. Let’s delve into the different materials available, focusing on their applications, advantages, and considerations.
Acrylic coatings are known for their versatility and are widely used due to their cost-effectiveness and solar reflectance. They are water-based, which limits their environmental impact by releasing fewer VOCs. According to a study from the Office of Energy Efficiency & Renewable Energy, acrylic coatings are particularly effective in climates with high UV exposure due to their excellent UV resistance. This makes them an ideal choice for properties in sunny regions, including parts of Palmetto. However, they aren’t the best in areas with heavy moisture, as they tend to lose thickness over time when exposed to ponds of water.
Silicone coatings stand out for their exceptional water resistance, making them suitable in regions with significant rainfall or consistent humidity. Popular for sealing roofs that collect water, silicone coatings provide strong adherence to different substrates, even in the presence of moisture. This retention ability is supported by findings in the Journal of Coatings Technology, which highlight silicone’s superior performance in preventing water infiltration. Nevertheless, they can attract dirt, causing a loss in reflectivity over time, which may necessitate periodic cleaning to maintain energy efficiency.
Polyurethane coatings offer excellent durability and impact resistance, making them perfect for areas subject to foot traffic or potential damage from hail. They are generally available in two types: aromatic and aliphatic. Aromatic polyurethanes are typically used for base coats due to their economical cost and toughness, while aliphatic polyurethanes, known for superior UV resistance and gloss retention, are often used as topcoats. The material’s robustness is highlighted in research by the American Chemical Society, which touts its utility in more demanding environments. However, they can be more costly, which should be weighed against budget constraints.
Another option to consider is butyl rubber coatings. This solvent-based material is praised for its strong tensile strength and ability to withstand ponding water. As noted by the Canadian Buildings Digest, butyl rubber coatings are highly effective for flat roofs commonly found on commercial properties. Their elastic nature makes them adept at expanding and contracting with the roof as temperatures vary, thus minimizing cracks and leaks. Yet, they have a higher initial cost and can be challenging to apply compared to other types.
Finally, there are bitumen-based coatings, often used in cold-process roofing applications. They emphasize versatility with their compatibility across a variety of surfaces. However, these coatings have higher VOC emissions, which may not align with stricter environmental standards or sustainability priorities. Utilizing data from a study by the International Journal of Building Pathology and Adaptation, bitumen is shown as efficient in specific scenarios but may fall short on broader environmental benefits unless the specific formula and application balance these factors adequately.
When considering the types of roof coatings for your property in Manatee County, assessing each material’s distinctive properties and environmental adaptability is crucial. Each type carries unique benefits tailored to specific climatic conditions and functional needs. It is also essential to consult with seasoned roofing experts to align your choice with both performance demands and budgetary goals. This selection process should aim for a solution that optimally integrates durability, cost-effectiveness, and sustainability to protect and enhance your commercial property.
Application Process: Expectations and Best Practices
Applying a roof coating to your commercial property is a strategic move to extend the life and efficiency of your roofing system. A successful roof coating process in Bradenton hinges on proper preparation and meticulous application, ensuring maximum performance and longevity.
First, start with a thorough inspection of the roof’s surface. This step involves identifying any needed repairs, such as fixing leaks, blisters, or cracks. An inspection prior to coating not only addresses existing issues but also ensures that the coating adheres properly. Typically, a professional roofing contractor will conduct a moisture survey to detect hidden damp areas that might affect the coating’s adhesion.
Once the roof has been inspected and repaired, cleaning is the next critical step. Debris, dirt, and oils can interfere with the coating’s ability to bond to the roof surface. A power wash is often recommended to remove any contaminants, allowing for an optimal coating application. This step can also involve cleaning agents specifically designed to tackle more stubborn build-ups. After washing, the roof should be left to dry completely, as any residual moisture can compromise the coating’s effectiveness.
The choice of primer is a crucial decision in the roof coating process. Primers enhance the bond between the roof surface and the coating. Depending on the roof’s material and the selected coating type, a specific primer may be recommended. For instance, metal roofs might require rust-inhibiting primers, while concrete roofs might need a sealant to smooth out the surface. Choosing the appropriate primer helps to prevent common problems such as peeling or flaking over time.
When applying the coating itself, uniform coverage is key to achieving desired results. Many coatings are applied using brushes, rollers, or spray equipment. Rollers are commonly used for large, open roof areas, while brushes might be needed for challenging corners or detailed work around roof fittings. Spraying, when done properly, allows for even distribution and can be more efficient on larger surfaces. It’s essential to follow manufacturer’s instructions for application thickness and ensure even coverage to avoid weak spots.
Temperature and weather conditions play a significant role in the application success. Most roof coatings should be applied in mild weather, as extreme temperatures can impact the drying and curing process. Windy days should be avoided, especially when spraying, to prevent over-spray and ensure the coating lands precisely on the intended areas. Ideally, select a day when the temperature is between 50-85°F, and the weather forecast is clear for at least two days post-application to allow the coating to set effectively.
Curing times vary based on the type of coating and environmental conditions. It’s advisable to keep foot traffic to a minimum during the curing period to avoid compromising the coating’s integrity. Full curing can take a few days, during which temperature and humidity can significantly influence the outcome.
Consistency in application and adherence to these practices ensure that the roof coating functions as intended, providing the desired protection and efficiency advancements. In Bradenton, partnering with knowledgeable professionals who understand the local climate and conditions can substantially impact the roof coating process, enhancing your investment’s return.
You might be asking
What are the benefits of applying a roof coating to a commercial building?
Roof coatings extend the lifespan of a roof by protecting it from UV damage and harsh weather. They can reduce energy costs by reflecting heat away from the building, helping to maintain a stable interior temperature. Additionally, roof coatings can prevent leaks and improve the overall aesthetics of the roof.
How do different roof coating materials compare?
Silicone coatings excel in UV protection and water resistance but can be more expensive. Acrylic coatings are cost-effective and ideal for reflective properties but may not hold up well in ponding water. Polyurethane coatings offer superior impact resistance and durability but can be more challenging to apply. Choosing the right material depends on the specific needs of your roof and climate.
How often should roof coatings be reapplied to maintain effectiveness?
Roof coatings generally need to be reapplied every 10 to 15 years, depending on the type of material, weather conditions, and wear. Regular inspections can help determine the appropriate timeline for reapplication, ensuring the roof remains in optimal condition.
Next Steps
Choosing the right roof coating for your commercial property in Manatee County involves a careful evaluation of your building’s needs, climate considerations, and budget constraints. Each material type, from acrylic to bitumen-based coatings, offers distinct advantages and challenges. It’s essential to weigh these factors against the specific environmental conditions your property faces, ensuring a choice that aligns with your long-term goals for energy efficiency and durability. Consulting with experienced roofing professionals will further refine the selection process, providing tailored guidance that aligns with both performance requirements and financial plans.
By taking these steps, you set the foundation for a robust roofing solution that not only protects your investment but also promotes sustainability. For those considering a commercial roof coating, partnering with Roofline Roofing offers a comprehensive approach to this investment. We invite you to reach out for a free consultation to discuss your specific needs. Our team of certified professionals is ready to guide you through the process, ensuring optimal performance and efficiency for your roofing system.
Contact Us
Use the form below to contact us or to schedule a free consultation.
I would highly recommend Roofline Roofing for any roofing needs. As a fellow business owner, their professionalism and efficiency stood out. They provided quality service, completed the job on time, and their pricing was fair. Very satisfied with their work!
-- Logan L.